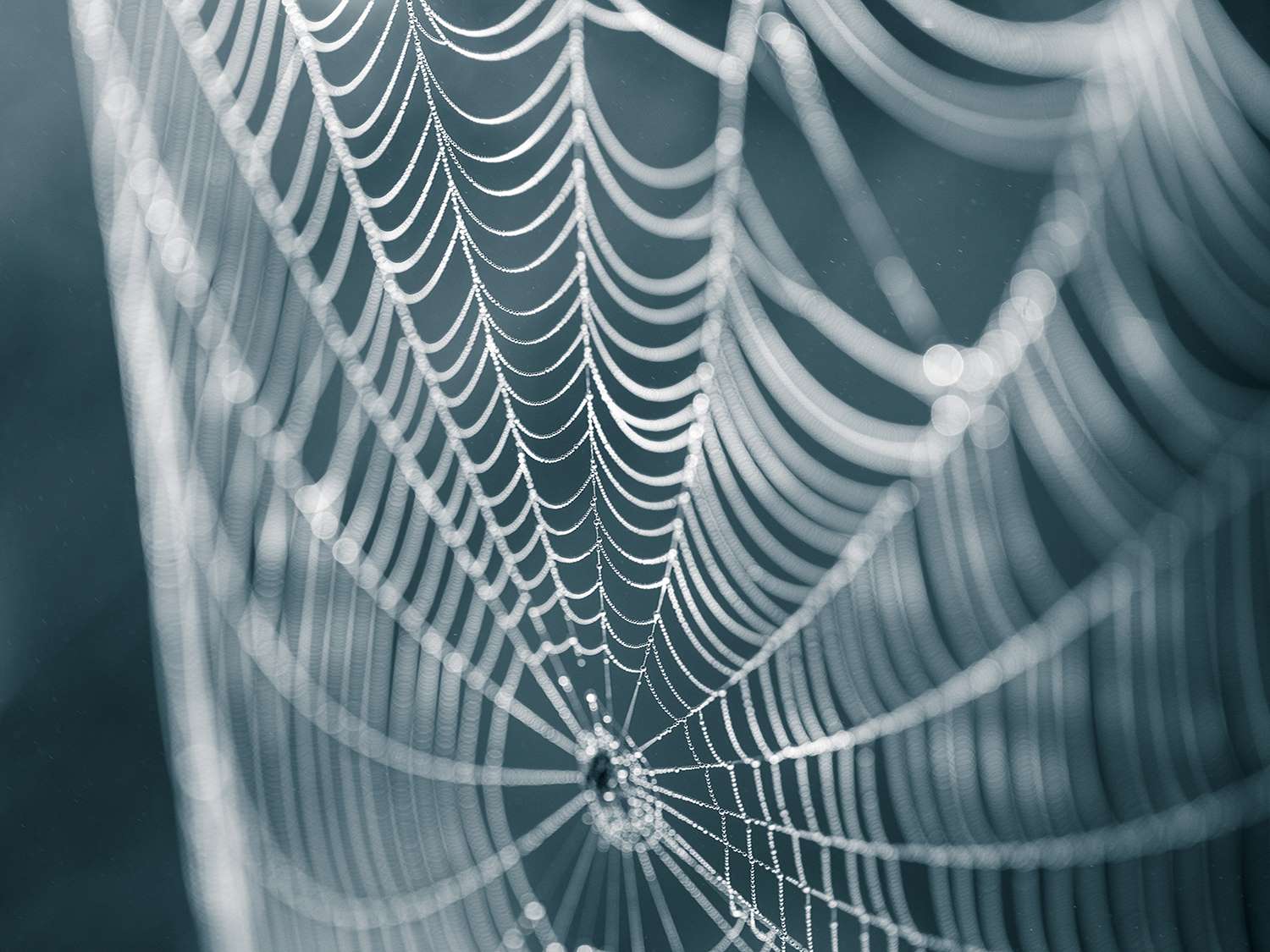
The advantageous properties of spider silk have long drawn interest for a myriad of applications. WTiN explores recent work from Universität Bayreuth, as well as developments from Spiber and Spintex, pertaining to textile use cases.
You have already accessed your 2 free articles this month although, we know you are keen to explore more.
The good news? We've got the perfect solution for you...
We've been working hard to enrich WTiN.com to ensure it delivers maximum value to our members. Let's take a look at how our membership features will support you in making informed business decisions:
-
WTiN.com Feature
Your Current Access
-
Insight
Limited
-
Reports
-
Company Analysis
-
Innovation Briefings
-
WTiN Digital Journals
-
News Hub
-
Watch & Textile Innivation Webinars, Fireside Chats & Podcast Episodes
Limited
-
WTiN Events
-
Discover
Digital Textile Hub
Nonwovens Hub
Smart Textiles Hub
Patents Hub
Digitalisation Hub -
AI-powered Insights
-
Watchlist
-
Membership
-
Unlimited
-
-
-
-
-
-
-
-
-
-
Unlock a bespoke solution-based membership proposal, just for you...