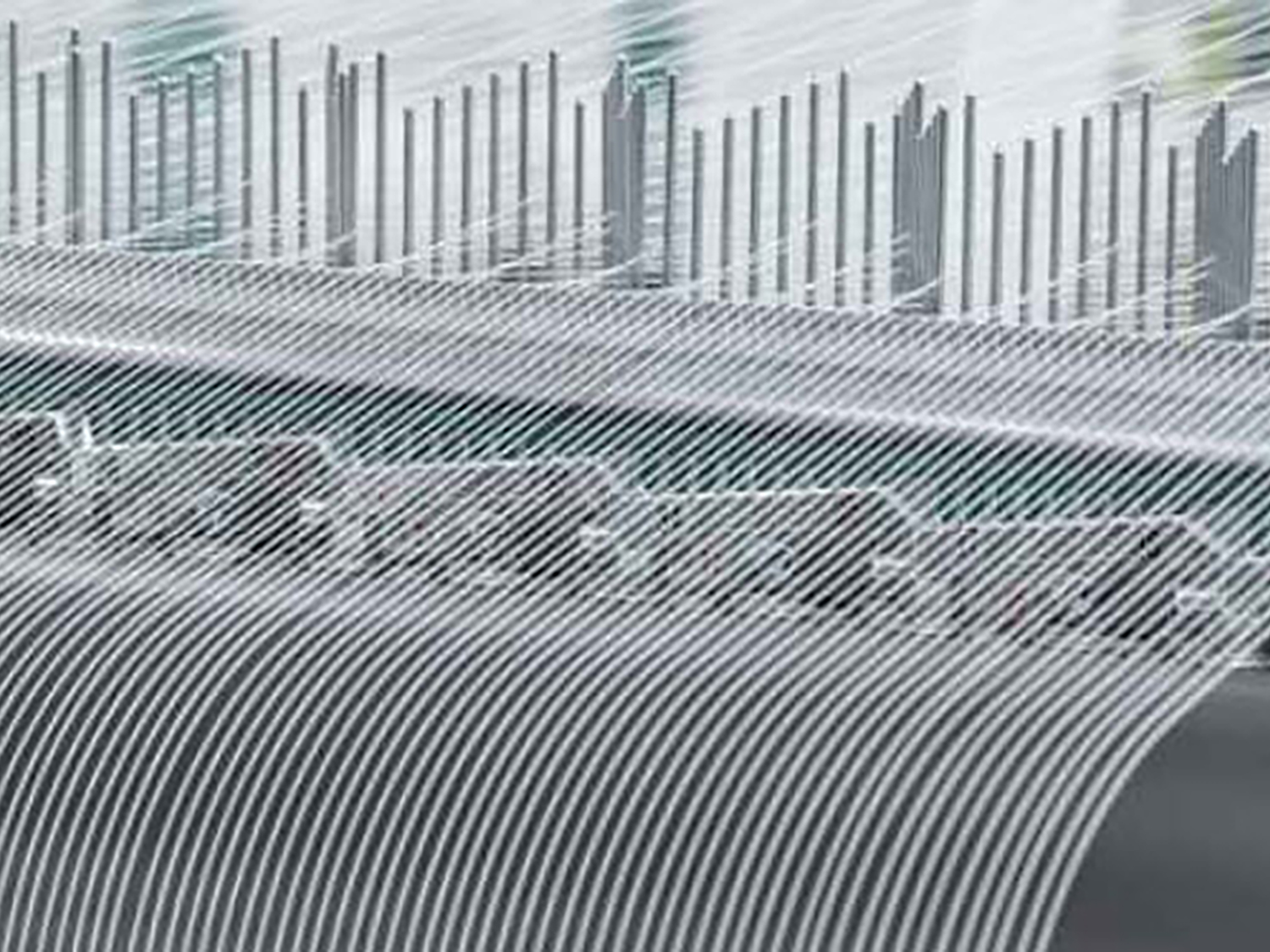
Sponsored by SNF
Abstract
A little more aware and informed of the impact of their purchases on the environment, today’s consumer pushes companies – particularly those in the textile industry – to take new production paths that minimise their environmental impact.
Of all the industries, the textile sector consumes the third-most most water: using 4% of the world’s drinking water. It is also the second-most polluting, generating 1.2bn tons of CO2 per year, which represents 2% of global greenhouse gas emissions.
In a bid to satisfy today’s more aware environmentally conscious consumers, global fashion brands have raised their awareness of their products’ environmental impact and are now imposing new standards and requirements on their suppliers that are more respectful of the environment.
These requirements focus not only on the toxicity of chemicals used in the textile manufacturing process, but also on the level of sustainable development, as well as environmental, social and economical ethics.
This transformation of the textile industry has already begun with the ban on certain chemicals, such as formaldehyde, and the use of digital printing, which consumes less water than conventional printing. But other manufacturing processes have evolved little or not at all, even if solutions exist and are sometimes insufficiently recognised.
Textile sizing is one example. This operation encapsulates yarns before the weaving stage to protect them from breakage and has been using the same products and techniques for more than 50 years, although it is one of the most polluting steps and represents 40 to 70% of the Chemical Oxygen Demand (COD) load of finishing mills.
I. STATE OF THE ART: SIZING CHEMICALS
A. What is sizing and its requirements?
The sizing process comes before the weaving stage and applies liquor to the surface of the yarn to strengthen it, reduce hairiness and avoid breakage in the weaving looms.
Adhesives and softeners are common combinations in sizing solutions. Sometimes anti-foaming agents and wetting agents are also required. Generally, up to 15-20% of sizing materials are added to the sizing solution, with 80-85% water. The solution preparation will depend on the textile mill’s yarn characteristics and the weaving loom’s technology.
Sizing liquor requires optimal distribution, for these reasons:
- Too much penetration, no surface coating
- Too much penetration, more size added to provide a surface coating
- Too little penetration, no anchoring of yarn structure
- Optimal distribution
B. What are the commonly used products in sizing?
Starch
Starch is one of the traditional sizing agents, as its hydroxyl groups allow a good adhesion to hydrophilic fibres such as cotton, viscose, etc. Commonly used starches are corn, wheat, potato, and tapioca. Among them, maize and wheat starch have better sizing performance and can be used for warp sizing. Various starch derivatives, such as oxidized starch, carboxymethyl starch, and cationic starch are also widely used in the sizing application.
The starch solution is suitable for sizing only after swelling and gelatinization at high temperatures (above 80°C) and forms a film when temperature decreases. But the viscosity is not always stable; the film is brittle and hard and prone to contamination by microorganisms.
Alginates
Alginate is a natural polymer formed by the condensation of β-D-mannuronic acid. Alginic acid produced by chemical processing is insoluble in water, but its sodium or ammonium salt becomes soluble and is called sodium alginate (or ammonium). Its aqueous solution has low concentration and high viscosity and can be used for sizing cotton and viscose yarns. But this material is now rarely used due to its inferior performance and high cost.
Cellulose derivatives
The most commonly used cellulose derivative is carboxymethyl cellulose (CMC), which is formed by the etherification of alkali cellulose with monochloroacetic acid. When the degree of substitution is more significant than 0.4, it is water-soluble and suitable for sizing cotton and viscose yarn. CMC aqueous solution has low concentration, high viscosity, poor permeability, good hygroscopicity and fine miscibility with other main slurries. Crude products have high salt content and are highly corrosive to machine parts, so they are unsuitable for sizing. Due to its high viscosity, re-viscosity, and cost reasons, it cannot be used as the primary slurry.
Polyvinyl alcohol (PVOH or PVA)
Commonly used polyvinyl alcohol (PVA or PVOH) can be classified following the polymerisation degree. High-degree polymerised PVOH is suitable for hydrophilic fibres, and low-degree PVA is ideal for hydrophobic fibres. In addition to a solid and flexible film, PVA can be mixed with other slurries to produce efficient sizing liquors.
The two main drawbacks are the environmental impact and the requirement for an enzyme-based desizing process. The non-degradability of its waste liquid during skewing has driven the trend to advocate “less and no PVA”. Europe and the US have proposed an import ban on PVA-sized fabrics.
Acrylic polymers
Acrylic polymers are a group of homopolymers of acrylic acid and its salts, copolymers of acrylamide and acrylic acid and homopolymers of acrylamide that can be anionic or non-ionic. This family of products possesses high hydrophilicity and an affinity to hydrophilic fibres and has been used as additives in sizing formulation in combination with starch derivatives or other sizing auxiliaries.
Polyacrylamide polymers are known to provide strength to sizing films, performing sizing film smoothness on the surface of the yarn and bringing low-breaking elongation. In contrast, high elongation is a property obtained by using polyacrylic salt polymers.
SNF developed a specific range of sizing polymers, “FLOSIZE™”, to combine the best properties to obtain optimal sizing compromises such as good resistance, film smoothness, and flexibility leading to high weaving productivity.
FLOSIZE™ polymers are readily soluble in water; desizing such products can be made even at room temperature without adding additives.
Unless PVA, they are also easy to remove from the water effluent because they are highly compatible with membrane water purification and can easily flocculate in the water treatment sludge.
Polyester resin
Water-soluble polyester is a polymer obtained by copolymerizing polyester monomers raw materials and adding water-based third monomers. Because of its affinity for polyester, it has been used as a sizing agent on polyester filament and staple fibre. It can be used also on cellulosic fibres to improve size adhesion.
II. SNF POLYMERS
SNF developed polymers that can work alone or blended with other sizing compounds to size hydrophilic fibres such as viscose yarns, cotton yarns and its blends to increase the sizing performance before the weaving step.
A combination of non-ionic and anionic polymers is required to achieve the best performance, and the initial recipe will depend mainly on the characteristics of the yarn to be sized: hairiness, count of the yarn, warp density, spinning type, and others.
The working process is eased as there are fewer quantities to handle and an easier desizing step thanks to the high solubility of the polymers.
The following table gives a comparison between the different sizing chemicals and different overriding parameters in the sizing application:
During the trials conducted in the field with FLOSIZE polymers, it was found that the performance against the usual products (combination of starch, PVA, and wax) is real: better performances were achieved once the sizing recipe had been adjusted to the sizing mill conditions.
In the following, we will study FLOSIZE polymers’ impact on three axes:
- Technical axis: What is the efficiency of FLOSIZE’s products against conventional sizing products?
- Financial axis: Are FLOSIZE’s products more costly than conventional sizing products?
- Environmental axis: Will FLOSIZE’s products be an environmental solution to reduce the COD in the effluents?
A. SNF sizing polymers: a technical solution
To analyse the performances of SNF polymers, we will study three examples of trials.
Trial N°1: PVOH replacement in cotton
The customer’s request was mainly to increase the sizing performances and to decrease the warp yarns breakages as we replaced the PVOH quantity with a recipe based on FLOSIZE™ products, as shown below.
Sizing results and weaving results were as shown below.
With this trial, CMPX breakage on warp yarns was reduced by 47% from 8.16 to only 4.3, with an increase in the loom efficiency from 78% to 82.5%.
Trial N° 2: PVOH replacement in a blend of polycotton
The customer request was to reduce the PVOH quantity and increase the sizing performances. SNF proposed a first trial:
After leading the first trial, the following results were obtained:
We observed a significant increase in the CMPX with 85.46% efficiency with the current recipe used by the customer based on PVOH and starch, mainly against 94.36% efficiency using SNF polymers.
But the customer expressed that his concern was mainly the warp breakage rather than the global efficiency of the weaving loom.
SNF proposed then a second trial as shown below.
The results obtained at the end of the trial are shown below.
With this second trial, CPMX breakage on warp yarns was reduced from 3.68 to only 1.57, with an increase in the loom efficiency from 85.46% to 86.25%. The final fabric quality was better with SNF recipes, decreasing defects like stop marks with higher and lower weft density, ladder effect, and oversizing.
The warp elongation was also improved from STD -2.86 to -0.92 on the first trial and 1.71 in the second trial with a similar warp tenacity result.
Trial N° 3: Solution for fine counts Ne80/1 dyed yarn.
A sizing trial operated on dyed yarns where the concern of the sizing mill was to reduce the cost of sizing operations and to obtain better performances.
Following the sizing trials, the results were as shown below.
With this trial, CPMX breakage on warp yarns was reduced by 76.6% from 8 to only 4.5, with a noticeable increase in the loom efficiency from 80% to 92.2%.
B. SNF sizing polymers: an environmental solution.
For the sizing application, environmentally optimised agents should be:
- Highly efficient with low add-on.
- Completely and easily removed from the fabric.
- Readily bio-eliminable (>80 % after seven days according to OECD-test 302 B).
COD (or Chemical Oxygen Demand) is the oxygen consumption by strong chemical oxidants to oxidize organic substances and mineral water. It assesses the pollution load of wastewater and is the primary measure for effluent discharge standards.
Additional benefits may be obtained by using sizing products with excellent performance and easier desizing steps, as Sizing agents are responsible for 50 to 70% of the COD load of textile wastewater in finishing mills.
Here is a table with average COD values for standard-sizing products used in the industry.
Trial N°1: PVOH replacement in cotton
Below is our approach to the first trial.
By using SNF sizing agents in both cases, the COD impact of the sizing effluents was reduced by 59%.
Trial N° 2: PVOH replacement in a blend of polycotton
In the case of the trials conducted, below are the results of COD for each recipe in each trial.
By using SNF sizing agents in both cases, the COD impact of the sizing effluents has been reduced by 47% in the first and 39% in the second trials.
Trial N° 3: solution for fine counts Ne80/1 dyed yarn
By using SNF sizing agents, the COD impact of the sizing effluents in this trial has been reduced by 58%.
Using SNF products allows the customer to highly reduce the COD impact on wastewater effluents.
Using SNF sizing polymers, the textile mills act for sustainable and greener development in textile production.
C. SNF Sizing polymers: An economical solution.
In such a competitive market, textile brands are squeezing textile-producing units to reduce prices by choosing low-cost countries instead of local production. Textile units must integrate the costs into their production but rely on the same processes used for years, even if sometimes some new and innovative solutions exist.
SNF polymers could be considered expensive in terms of the price per kg of the product itself, but we looked at the bigger picture: the impact of a sizing and weaving unit on the price of a year’s production?
We will consider in this exercise the following costs:
FLOSIZE 4.0
PVOH 3.0
Native starch 0.5
Acrylic liquid 0.8
Acrylic polymer 4.0
Modified starch (or cellulose) 1.0
Wax 3.0
Trial N°1: PVOH replacement in cotton
Following the trial conditions, the sizing cost of the recipe would be as shown below.
The cost calculations of a yearly production will be as shown below.
The recipe cost with FLOSIZE™ products was 14.5% higher in sizing cost at first glance. But if we go through a yearly production and evaluate the total costs when changing to the SNF recipe in this sizing trial, the sizing factory had a positive balance, with a profit of US$10.000. Even if the sizing cost was increased by US$25.000, a profit of US$35.000 was done on the fabric production due to the high performance of FLOSIZE™ compounds.
And additional savings could be made in the subsequent processes, such as in the desizing step, as FLOSIZE products are water soluble and have no need for enzymes when used alone to desize the fabric.
Trial N°2: PVOH replacement for cotton yarns
Following the trial conditions, the sizing cost of the recipe would be as shown below.
Cost calculations of a yearly production will be as shown below.
We observed that the SNF-based recipe is 8% higher. But based on the total year production, due to the high efficiency obtained 94.36% instead of 84.3%, the yearly fabric production increased by 10%, increasing the fabric’s value by 10% and reducing the cost of sizing by 4.4%.
In this trial, global sizing costs were reduced by 2.7%, and fabric production increased by 1%
Trial N° 3: solution for fine counts Ne80/1 dyed yarn.
In this trial with fine counts, fabric price is crucial as it is meant for the fashion industry.
The recipe price was 30% higher when using SNF polymers, but the handling quantities were three times lower. Also, the weaving efficiency increased from 80% to 92.2% using FLOSIZE products, and the productivity and fabric value also increased. The balance between an increase of size cost was US$30,000/year, while the additional profits on the fabric were about US$95,000.
III. CONCLUSION
After reviewing the technical, environmental, and economic aspects that can push textile mills to opt for such a process, SNF polymers responded positively to all three of these points.
The FLOSIZE™ products can be an excellent substitute for the conventional sizing auxiliaries in the industry, where customers would handle fewer chemicals in the sizing mill, fewer effluents and have better efficiency and cost saving.
Have your say. Tweet and follow us @WTiNcomment